Watchmaking
NEO-FUGU®: the ERP designed for watch manufacturers.
Designed to meet the unique requirements of watch manufacturers, NEO-FUGU® supports these players of excellence in managing their complex processes.
The watchmaker, the craftsman of time, is a professional of great precision and unfailing patience. He works on luxury watches, veritable mechanical jewels, where every component is a marvel of engineering.
His job involves assembling, adjusting, repairing and sometimes even creating these complex mechanisms from scratch. Using meticulous tools, he manipulates tiny, fragile parts, often invisible to the naked eye, to bring a timepiece to life. The watchmaker is a technician, an artist and a historian all rolled into one, as he often works on old timepieces that he restores with respect. It is the guarantor of the transmission of ancestral know-how and a passion for measuring time.
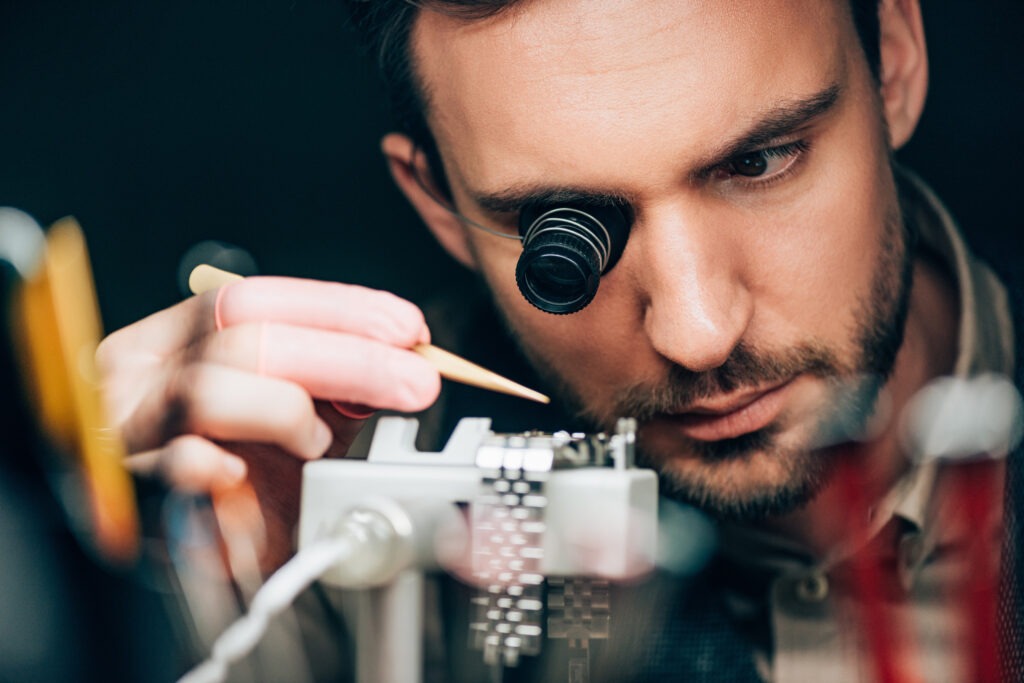
⌚ Our references
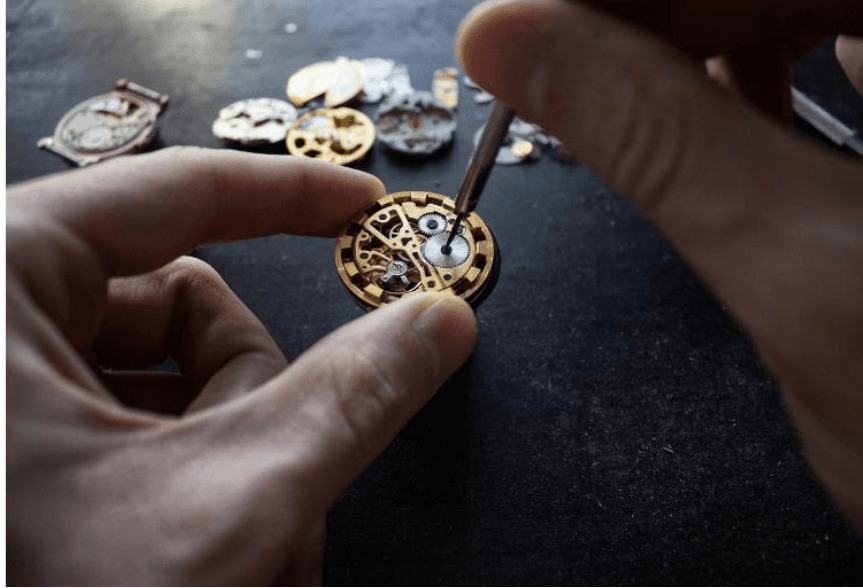
His mastery of specific tools, such as the binocular magnifier and the precision screwdriver, enables him to work on minute parts with incredible dexterity. Every move is meticulous, every adjustment meticulous, because a single speck of dust can disrupt the operation of a movement…
Sculpting time, an art that requires patience and meticulousness...
1. Conception
The watch’s design is developed taking into account trends, materials and desired functionalities. Detailed drawings are then made for each component of the watch, from the movement to the case.
CAD is also used in the watchmaking industry. It enables every component of a watch to be modelled in 3D with extreme precision, from the case to the smallest cogs. These virtual models make it possible to simulate the operation of the mechanism even before it is manufactured, guaranteeing optimum precision. Designers can easily visualise and modify their creations, speeding up the design process.
2. Manufacture of the components
The heart of the watch, the movement, is made from high-precision metal parts. Each component (gear train, barrel, balance wheel, balance spring, etc.) is machined with extreme precision.
The case, which protects the movement, is generally made of stainless steel, gold or other precious metals and is sometimes decorated (engraving, satin-finishing).
The dial is made of different materials (enamel, mother-of-pearl, metal) and decorated with hour-markers, numerals and hands.
The strap can be made of metal, leather or other materials.
3. Movement assembly
The various parts of the movement must then be assembled with extreme precision, following a precise order : pre-assembly of components, assembly of the barrel, assembly of the gear train, assembly of the escapement, assembly of the regulating organ (balance wheel and spiral) then final assembly.
The movement of a watch is adjusted to ensure optimum precision. The balance wheel, which controls the frequency of oscillation, is adjusted to the nearest micron.
4. Movement decoration
The edges of the components are ‘bevelled’ to give an aesthetic appearance and make assembly easier, and some surfaces are beaded to create a neat finishing effect.
There are also precise finishing techniques such as guilloché and chasing, and decorations that are characteristic of fine watchmaking, such as the côtes de Genève, which consist of parallel lines engraved on the movement’s bridges.
5. Watch assembly
Once the movement has been assembled and adjusted, it is gently inserted into the case. The choice of case material (stainless steel, gold, titanium, etc.) influences the weight, strength and appearance of the watch. The back of the case is then screwed or clipped on to ensure a primary seal.
The dial is fixed to the movement using different fixing techniques (screws, clips, glue) depending on the type of dial (metal, enamel, mother-of-pearl, etc.). The hands, hour-markers, numerals and other decorative elements are applied to the dial.
The watchmaker has fitted the watch with strategically placed seals : between the case and the bezel, between the crown and the crown tube, and between the case back and the case itself.
The choice of strap is essential for the comfort and aesthetics of the watch, and is fixed to the case using bars or screws.
6. Quality control
This stage is crucial in the manufacture of any watch, as it guarantees the perfection of the finished product. After assembly, the watch undergoes a series of rigorous tests :
- water-resistance, movement precision, shock-resistance, specific functions such as chronograph or date.
At the same time, a meticulous visual inspection is carried out to check the alignment of the hands, the symmetry of the case and the quality of the finish.
Finally, a final quality check is carried out by an experienced watchmaker. He checks the entire watch to ensure that it meets the highest quality standards.
Each watch that leaves the workshop must be an exceptional product that combines precision, reliability and aesthetics.